Process receipts and deliveries in two steps¶
Depending on a company’s needs, receiving and shipping products in and out of the warehouse might require multi-step operations. In Odoo Inventory, this can be done using Multi-Step Routes.
In the two-step receipt process, products are received in an input area, then transferred to stock. This kind of process for incoming shipments might be beneficial for warehouses with specific storage locations, such as freezers and refrigerators, secured locked areas, or special aisles and shelves.
Products can be sorted according to where they are going to be stored, and employees can stock all the products going to a specific location. The products are not available for further processing, until they are transferred into stock.
In the two-step delivery process, products are first picked from their respective location in the warehouse, then transferred to an output location before being shipped to the customer.
This might be beneficial for companies using a First In, First Out (FIFO), Last In, First Out (LIFO), or First Expired, First Out (FEFO) removal strategy.
Tip
Incoming and outgoing shipments do not need to be configured with the same amount of steps.
For example, a warehouse’s settings can be configured so products can be received in two steps (input + stock), and delivered in three steps (pick + pack + ship).
Configuration¶
In Odoo Inventory, both incoming and outgoing shipments are configured to process in one step, by default. To change these settings, the Multi-Step Routes feature must be enabled.
To enable Multi-Step Routes, navigate to Warehouse section, tick the checkbox next to Multi-Step Routes, and click Save. Doing so also activates the Storage Locations feature.
. Under the
Next, configure a warehouse for two-step receipts and deliveries. Navigate to
, and select a warehouse to edit.Under the Warehouse Configuration tab, set Incoming Shipments to Receive goods in input and then stock (2 steps), and set Outgoing Shipments to Send goods in output and then deliver (2 steps).

Note
Selecting two-step receipts and deliveries automatically creates new Input and Output
warehouse locations in the database, named WH/Input
and WH/Output
, respectively.
To rename or edit these locations, navigate to
, and select the desired location.On the location’s form, change the Location Name, and make any other necessary changes.
Process receipt in two steps (input + stock)¶
When products are received in two steps, they first move from the vendor location to an input location. Then, they move from the input location to warehouse stock in the database, upon validation of a purchase order (PO), and a subsequent internal transfer.
Create purchase order¶
To create a PO, navigate to the New. This opens a blank Request for Quotation (RfQ) form.
, and clickAdd a vendor in the Vendor field. Then, fill out the various fields on the RfQ, as necessary.
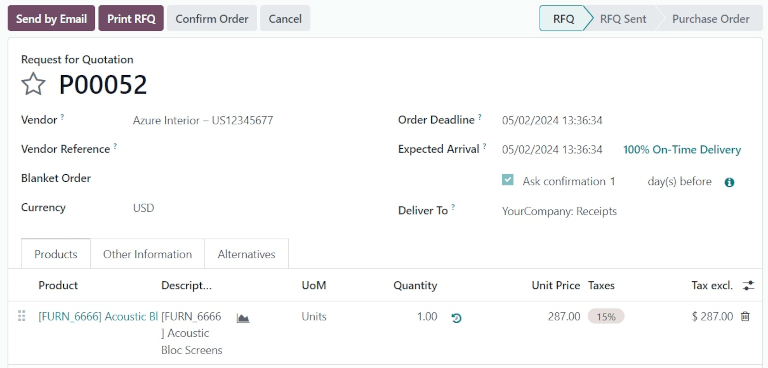
Under the Products tab, click Add a product, and select a product to add to the RfQ.
Once ready, click Confirm Order. This moves the RfQ to the Purchase Order stage.
Once the PO is confirmed, a Receipt smart button appears at the top of the form. Clicking the smart button opens the warehouse receipt (WH/IN) form.

Tip
For businesses with multiple warehouses that have different step configurations, the Deliver To field on the PO form must be specified as the correct input location connected to the two-step warehouse.
This can be done by selecting the warehouse from the drop-down menu that includes the Receipts
label at the end of the name.
Process receipt¶
From the warehouse receipt form, the products ordered can be received into the warehouse. To receive the products, click Validate. Once validated, the receipt moves to the Done stage, and the products move to the WH/Input location.

Click back to the PO (via the breadcrumbs, at the top of the form) to view the PO form. On the product line, the quantity in the Received column now matches the ordered Quantity.
Process internal transfer¶
Once the receipt is validated, an internal transfer is created and ready to process.
To view the internal transfer, navigate to the Internal Transfers task card.
, and locate theClick the # To Process button on the task card to reveal a list of all internal transfers to process, and select the transfer associated with the previously validated receipt.
Once ready, click Validate to complete the transfer, and move the product from WH/Input to WH/Stock.
Once the transfer is validated, the products enter inventory, and are available for customer deliveries or manufacturing orders.

Process delivery order in two steps (pick + ship)¶
When products are delivered in two steps, they move from warehouse stock to an output location. Then, they move from the output location to a customer location in the database, upon validation of a picking order, and a subsequent delivery order (DO).
Create sales order¶
To create a SO, navigate to the New. This opens a blank sales quotation form.
, and clickAdd a customer in the Customer field. Then, fill out the various fields on the sales quotation form, as necessary.

Under the Order Lines tab, click Add a product, and select a product to add to the sales order quotation.
Once ready, click Confirm. This moves the quotation to the Sales Order stage.
Once the SO is confirmed, a Delivery smart button appears at the top of the form. Clicking the smart button opens the warehouse delivery (WH/OUT) form.

Process picking¶
Once the sales order is confirmed, a picking order is generated and ready to process.
To complete the picking, navigate to the Inventory app, and locate the Pick task card on the Inventory Overview dashboard. Alternatively, the picking order can also be accessed via the Delivery smart button at the top of the sales order form.
From the Inventory Overview page, click the # To Process button on the Pick task card. This reveals a list of all pickings to process.
Click on the picking (WH/PICK) operation associated with the sales order to reveal the picking order.

Manually set the quantity by changing the value in the Quantity column, to match the value in the Demand column.
Once ready, click Validate to complete the picking, and move the product from WH/Stock to WH/Output.
Process delivery¶
Once the picking is validated, a delivery order is created, and ready to process. Clicking the Delivery smart button on the sales order form reveals the newly created delivery order.
Alternatively, to view the delivery order, navigate back to the Inventory Overview page, via the breadcrumbs, and locate the Delivery Orders task card.
Click the # To Process button on the task card to reveal a list of all delivery orders to process, and select the order associated with the previously validated picking.

To deliver the products, change the value in the Quantity field to match the ordered quantity in the Demand field.
Once ready, click Validate. Once validated, the delivery order moves to the Done stage.